Close Collaboration With Customers Brings Job Shop Success
Contract machining operations win when they collaborate closely and openly with customers.
Share




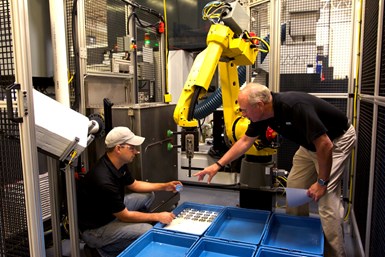
Tony Staub (right), founder, Staub Precision, offers automation insight to an employee.
Photo Credit: Staub Precision Machine Inc.
What does it mean to be “in the room where it happens?” Readers who have seen the play Hamilton likely understand. The play tells the story of how, in the 18th century, our nation’s capital moved from New York to Washington, D.C. It was a political compromise. The high-powered meeting was private and unless you were “in the room where it happened,” you had no voice, no input and no certainty of exactly what went down.
We are in the business of producing parts to customer specifications — we do not produce or sell a product ourselves. Our success depends wholly on the success of our customers, and the better job we do for them, the more likely they are to be successful. When our customers invite us to the room where decisions are made, we are in a great position to excel for them. We’ve formed partnerships with some customers where we both contribute to the part design and manufacturing process. We have a seat at their table, and they have a seat at ours. Our best partnerships are those where we can collaborate.
For instance, we have a large aerospace customer that is world-renown for its expertise in numerous fields. We are dwarfed by them in terms of staffing size, sales volume and certainly higher-education degrees. However, our expertise is in working out manufacturing solutions, and we are not afraid to raise our hand, ask for help and readily accept input.
It’s interesting to see how this relationship has developed. Ten years ago, it was easy to feel intimidated by the sheer size and success of this customer. It develops systems for the highest level of commercial and governmental clients. Some of their work is top secret. Yet about a decade ago, the company came to our small operation with a troublesome project. It needed a vendor to work on numerous aircraft components, and came to us because of our reputation for quantity machining.
The project fit our expertise. We were able to machine the parts required but they wanted more. They wanted the parts completely finished which included painting, plating, deburring and helicoiling — all things that were not in our wheelhouse. It was a struggle trying to satisfy them and there were many times where we questioned why we were losing money just to play the game. However, they stood by, encouraging us, and sent in personnel for troubleshooting and training. We worked together to find solutions and slowly conquered these challenges. Today, we produce thousands of these parts and we do it routinely and profitably. Collaborating with our customer contributed to the project’s success. They deserve a lot of credit for our success.
Our first opportunity with this customer, our dedication and our willingness to work with them earned us a reputation within their corporate walls. Two years ago, they came to us with yet another challenge. The company sought a vendor to machine parts for a long-standing, critical product. It was after a pristine part — a part which meets the stringent requirements of the aerospace industry. The part was seemingly easy to machine but tough on tool wear. The material was the main challenge. The project included stamping and forming before we ever got to machining, which was not in our core competency. However, the customer targeted us and us alone. Representatives came to us and encouraged us to take on the job producing ten item variations and thousands of individual parts. The work would likely last for years, maybe decades — we were intrigued.
The project started off slowly last year, but production has ramped up. Now, we are shipping hundreds of parts. However, we are not up to full production and the project is not yet cash-flow positive either. The customer is quick to warn us when we’re going down the wrong path. We experiment with various tool designs, manufacturing sequences and clamping methods and we’ve made different workholding fixtures. Through all this, the customer support our efforts. We are able to openly discuss issues, regardless of impact to cost.
We continue to work together. The project is going well, and we are overcoming the manufacturing challenges by collaborating. There are regular meetings for manufacturing reports. We discuss challenges and we take turns serving the ball. Inspection is the latest challenge we face: we need 100% inspection on many of the features and it has become a bottleneck. Our problem is their problem, so we will sit down to talk — again.
We will overcome all of the challenges that come with this project. And we will turn it into a profitable job. It takes time, dedication and perseverance but it works much better when we both have a seat “in the room where it happens.”
Related Content
How I Made It: Nushrat Ahmed: CNC Swiss Operator
By day, 21-year-old Nushrat Ahmed is a CNC Swiss operator making automotive parts. By night, she handcrafts crocheted items.
Read MoreThe Power of Practical Demonstrations and Projects
Practical work has served Bridgerland Technical College both in preparing its current students for manufacturing jobs and in appealing to new generations of potential machinists.
Read MoreManufacturing Technology and Training in Europe
NTMA’s European Tech Tour exposed attendees to the latest technology and traditional training methods used by European manufacturers.
Read MoreInside Machineosaurus: Unique Job Shop with Dinosaur-Named CNC Machines, Four-Day Workweek & High-Precision Machining
Take a tour of Machineosaurus, a Massachusetts machine shop where every CNC machine is named after a dinosaur!
Read MoreRead Next
Machine Shop MBA
Making Chips and 91ÊÓÆµÍøÕ¾ÎÛ are teaming up for a new podcast series called Machine Shop MBA—designed to help manufacturers measure their success against the industry’s best. Through the lens of the Top Shops benchmarking program, the series explores the KPIs that set high-performing shops apart, from machine utilization and first-pass yield to employee engagement and revenue per employee.
Read MoreAMRs Are Moving Into Manufacturing: 4 Considerations for Implementation
AMRs can provide a flexible, easy-to-use automation platform so long as manufacturers choose a suitable task and prepare their facilities.
Read MoreLast Chance! 2025 Top Shops Benchmarking Survey Still Open Through April 30
Don’t miss out! 91ÊÓÆµÍøÕ¾ÎÛ's Top Shops Benchmarking Survey is still open — but not for long. This is your last chance to a receive free, customized benchmarking report that includes actionable feedback across several shopfloor and business metrics.
Read More