JTEKT Technology Days Showcases Synergies
The event took place following the company’s completion of its new showroom and decision to merge several of its brands under the JTEKT name.
Share




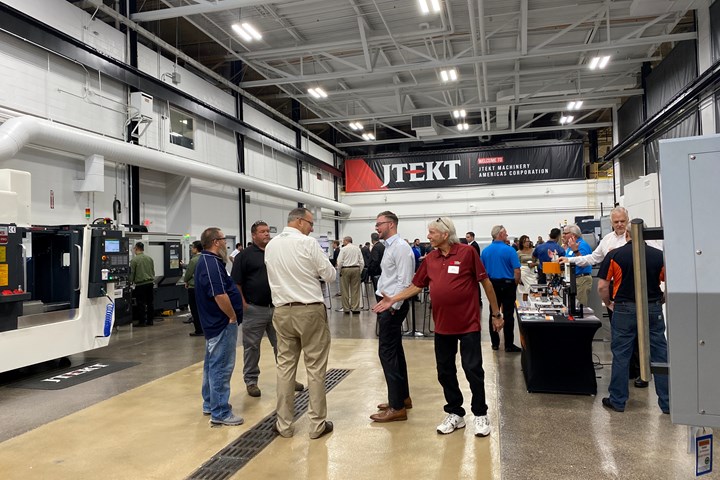
JTEKT held its Technology Days event at the new customer showroom at its headquarters in Arlington Heights, Illinois.
JTEKT had several things to celebrate at its Technology Days, held Sept. 14 and 15 at its Arlington Heights, Illinois headquarters. According to JTEKT President Mike Defer, not only was the event meant to show off its renovated facility and new customer showroom, it was a way to showcase collaboration opportunities between its brands and partners. The company recently brought several of its brands, including Toyoda and its automotive component manufacturing group, under the JTEKT name in a move that’s meant to reduce confusion and highlight synergies.
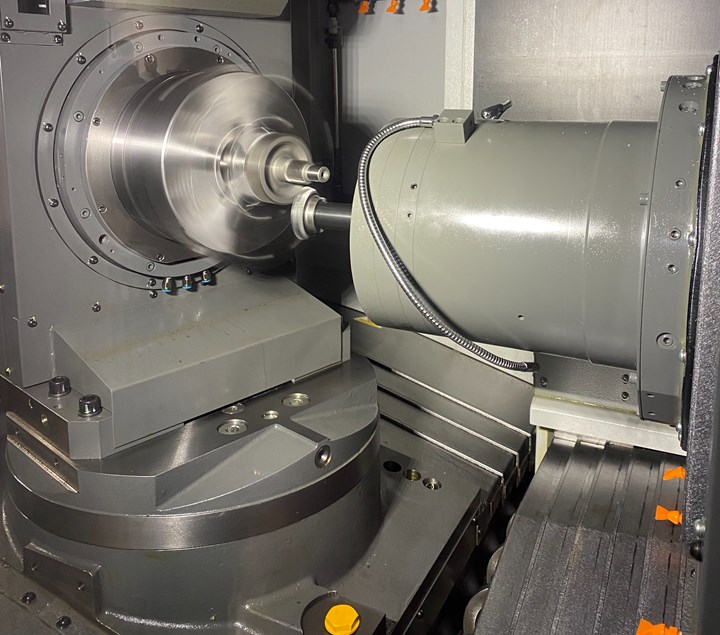
One theme of the event was the synergy between JTEKT’s brands and partners. This all-in-one GS200H gearmaking machine was originally designed for Torsen, a JTEKT company that produces helical gear torque-sensing differentials for the automotive industry.
One machine on the floor that demonstrated the benefits of this decision was the GS200H gearmaking machine. Originally designed for Torsen, a JTEKT company that produces helical gear torque-sensing differentials for the automotive industry, the GS200H is an all-in-one gear manufacturing solution with skiving, hobbing, drilling, milling and tapping capabilities. Traditional gearmaking requires multiple processes, and combining them into one platform can improve cycle times and part quality.
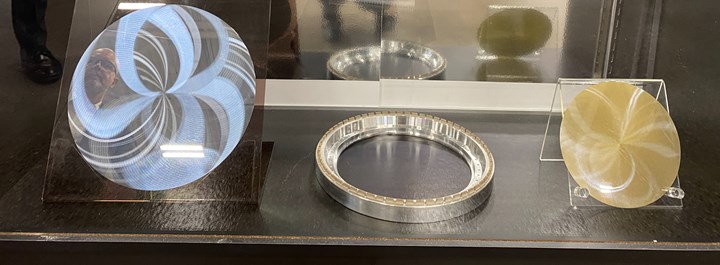
This display of silicon and silicon carbide parts represented JTEKT’s solutions for the semiconductor industry. It offers the R631DF single-spindle vertical grinder for silicon carbide and the DXSG320 horizontal double-disc grinding machine for silicon.
JTEKT was also promoting its grinding machines for semiconductor wafers in anticipation of an increase in demand for manufacturing solutions from this market. Although the machines themselves weren’t on display, the company showcased sample parts from two machines. The R631DF is a single-spindle vertical grinder with a vacuum chuck, designed for grinding silicon carbide. This material is so hard and brittle that full grinding pressure will crack the part. Instead, the machine uses “ultrasonic grinding,” where the grinding wheel is coming in and out of contact with the part in sort of a pecking motion. The DXSG320, on the other hand, is a horizontal double-disc grinding machine that grinds both sides of a silicon wafer at the same time. Both can be automated with a cassette-based automation system that loads the part, flips it, removes it and cleans it before returning it to the cassette. The DXSG320 also has an optional overhead transfer system.
Automation was present in other forms as well. One solution on display was JTEKT’s flexible manufacturing system (FMS) with a pallet automation system. Marketing manager John Quick explained that the company now integrates these systems at the factory, treating the pallet system and machine tool as one unit to reduce customer downtime and save costs. JTEKT was also featuring its RL7, an “out-of-the-box” engineered machine tending system with a full industrial robot arm.
The event also featured products from JTEKT’s partner companies, including Taiwan Takisawa, Mitsui Seiki and . Its relationship with AMG is enabling JTEKT to step into the additive manufacturing space through AMG’s brand. Amace offers two powder bed fusion machines, the STLR-180 and STLR-400, which can print 12 materials, including aluminum.
Related Content
Which Approach to Automation Fits Your CNC Machine Tool?
Choosing the right automation to pair with a CNC machine tool cell means weighing various factors, as this fabrication business has learned well.
Read MoreSame Headcount, Double the Sales: Successful Job Shop Automation
Doubling sales requires more than just robots. Pro Products’ staff works in tandem with robots, performing inspection and other value-added activities.
Read MoreTranslating a Prototyping Mindset to Production
The experimental mindset that benefited BDE Manufacturing Technologies as a prototype job shop has given it an adaptable edge as a production facility.
Read MoreHow to Accelerate Robotic Deburring & Automated Material Removal
Pairing automation with air-driven motors that push cutting tool speeds up to 65,000 RPM with no duty cycle can dramatically improve throughput and improve finishing.
Read MoreRead Next
Last Chance! 2025 Top Shops Benchmarking Survey Still Open Through April 30
Don’t miss out! 91ÊÓÆµÍøÕ¾ÎÛ's Top Shops Benchmarking Survey is still open — but not for long. This is your last chance to a receive free, customized benchmarking report that includes actionable feedback across several shopfloor and business metrics.
Read MoreMachine Shop MBA
Making Chips and 91ÊÓÆµÍøÕ¾ÎÛ are teaming up for a new podcast series called Machine Shop MBA—designed to help manufacturers measure their success against the industry’s best. Through the lens of the Top Shops benchmarking program, the series explores the KPIs that set high-performing shops apart, from machine utilization and first-pass yield to employee engagement and revenue per employee.
Read MoreAMRs Are Moving Into Manufacturing: Considerations for Implementation
AMRs can provide a flexible, easy-to-use automation platform so long as manufacturers choose a suitable task and prepare their facilities.
Read More