Arch Cutting Tools Acquires Custom Carbide Cutter Inc.
The acquisition adds Custom Carbide Cutter’s experience with specialty carbide micro tools and high-performance burrs to Arch Cutting Tool’s portfolio.
Share




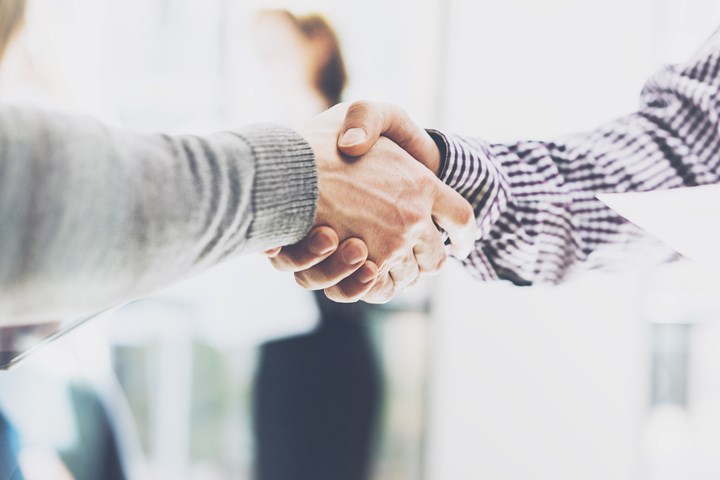
Arch Cutting Tools Corp. (Arch), a manufacturer of high-performance custom tooling, is acquiring Custom Carbide Cutter Inc. (CCCI), a provider of cutting tools to manufacturers and distributors located in Cincinnati.
"I am proud to announce the addition of Custom Carbide Cutter to the Arch Cutting Tools team,” says Jeff Cederstrom, Arch Cutting Tools divisional president. "Custom Carbide's experience in specialty carbide micro tools and high-performance burs sets them apart in the industry and compliments the Arch offering.”
Arch is based in Bloomfield Hills, Michigan, and serves the medical, aerospace, defense, automotive, energy, agriculture and general industrial markets. As a mid-sized, full service cutting tool manufacturer, Arch has facilities across the United States, and the company says it is dedicated to engineering high-performance standard and custom tooling.
“We are excited to offer these additional domestic manufacturing capabilities to the growing Arch customer base, especially the micro tool application expertise, as this is a rapidly expanding segment of the industry. Steve and Dena Long have assembled a talented team, and we look forward to building on Custom Carbide’s longstanding customer relationships with additional products and services,” Cederstrom adds.
CCCI was established in 1983 to provide cutting tools for local companies in the Cincinnati area but has since grown to service customers around the world. It specializes in serving the automotive and aerospace industries along with shipyards and medical facilities.
“The acquisition by Arch Cutting Tools will help us keep pace with this ever-changing industry,” says Steve Long, CCCI president. “It will give us access to additional support and guidance for our highly-skilled employees and help us continue developing our manufacturing processes.”
Related Content
-
Lean Approach to Automated Machine Tending Delivers Quicker Paths to Success
Almost any shop can automate at least some of its production, even in low-volume, high-mix applications. The key to getting started is finding the simplest solutions that fit your requirements. It helps to work with an automation partner that understands your needs.
-
Form Tapping Improves Tool Life, Costs
Moving from cut tapping to form tapping for a notable application cut tooling costs at Siemens Energy and increased tool life a hundredfold.
-
Quick-Change Tool Heads Reduce Setup on Swiss-Type Turning Centers
This new quick-change tooling system enables shops to get more production from their Swiss turning centers through reduced tool setup time and matches the performance of a solid tool.