SMW Autoblok Acquires Tecnomagnete
Tecnomagnete is said to have invented the use of permanent magnetic systems for component clamping, plastic injection molding, stamping and lifting.
Share





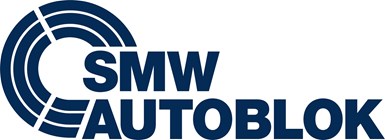
SMW Autoblok Group, a leader in the design, engineering and manufacturing of premium workholding solutions for the industrial market, has acquired Tecnomagnete, a leading manufacturer of permanent electromagnetic clamping and lifting systems. Tecnomagnete is said to have invented the use of these types of magnetic systems for a new way of holding and lifting parts.
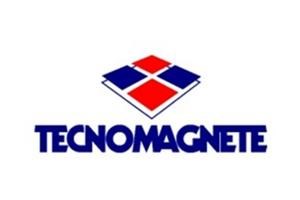
Tecnomagnete, headquartered in Milan, Italy, has divisions located in the U.S., Germany, France and China, and serves the manufacturing and material handling industries with products manufactured for sectors including automotive, die and mold, oil and gas, energy, infrastructure, steel, shipbuilding, plastics and transportation. The company’s advanced technology reportedly enabled it to invent the use of permanent magnetic systems for component clamping, plastic injection molding, stamping and lifting.
“We are extremely excited about acquiring Tecnomagnete and offering even more specialized workholding capabilities to help customers with their diverse manufacturing needs,” says Larry Robbins, president of SMW Autoblok’s commercial division. “[Its] technologies are a perfect complement to our growing product offering, and we look forward to what the future holds.”
SMW Autoblok’s new Mag Autoblok division includes a full line of permanent electromagnetic chucking systems for quick and flexible workholding on horizontal and vertical milling machines, vertical turning centers, flexible manufacturing systems, grinding machines, EDMs and more. A full line of magnetic lifters for loading and unloading workpieces is also offered.
With the addition of Tecnomagnete, SMW Autoblok says its portfolio supports both new and existing customers by providing solutions to achieve greater productivity, flexibility and safety in an expansive range of manufacturing operations.
Related Content
-
Medical Shop Performs Lights-Out Production in Five-Axes
Moving to five-axis machining enabled this shop to dramatically reduce setup time and increase lights-out capacity, but success relied on the right combination of workholding and automation.
-
Lean Approach to Automated Machine Tending Delivers Quicker Paths to Success
Almost any shop can automate at least some of its production, even in low-volume, high-mix applications. The key to getting started is finding the simplest solutions that fit your requirements. It helps to work with an automation partner that understands your needs.
-
Parts and Programs: Setup for Success
Tips for program and work setups that can simplify adjustments and troubleshooting.