Bluco Corp. Releases Modular Fixturing Line for Extra-Large Parts
Bluco’s 8024 Modular Fixturing Series has 80 mm grid spacing and 24 mm nominal bore size. The company’s application engineers will use the new 8024 series to design custom solutions for manufacturers of large parts.
Share





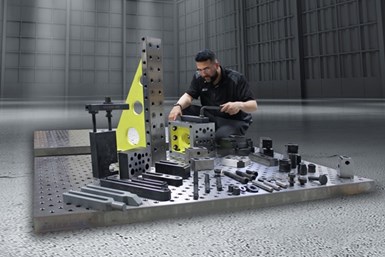
Bluco Corporation has released a modular fixturing system designed to hold extra-large parts for CNC machining. The 8024 Modular Fixturing Series has 80-mm grid spacing and 24-mm nominal bore size. According to the company, the system is the largest modular fixturing solution it has produced to date, and the first complete line of its kind.
Bluco’s application engineers will use the new 8024 series to design solutions for manufacturers of large parts. The company says it designed the system for customers in industries such as agriculture, mining, locomotive, oil & gas or defense who routinely deal with large parts.
According to the Bluco, bigger systems require fewer components to do the same job, which reduces fixture setup time. The larger size of the systems also makes it easier to visually identify that each component is placed correctly.

In addition, the system is designed to reduces downtime between jobs via the baseplate that’s part of every system. According to Garrett Gordon, Bluco senior engineer, the company customizes a modular baseplate to fit each customers machine bed. Then, instead of bolting a part directly to the machine bed, where users can only guarantee accuracy in one direction, users bolt it to a plate that offers accuracy in every direction.
The system is said to feature accuracy of ±0.015 mm (±0.0006"), precision-ground components, reliable clamping against a single component and a kit of extra-large modular components to fixture multiple parts. Bluco manufactures a large portion of the new system’s components, including the baseplates, in-house at its facility.
Related Content
-
Machining Vektek Hydraulic Swing Clamp Bodies Using Royal Products Collet Fixtures
A study in repeatable and flexible workholding by one OEM for another.
-
Lean Approach to Automated Machine Tending Delivers Quicker Paths to Success
Almost any shop can automate at least some of its production, even in low-volume, high-mix applications. The key to getting started is finding the simplest solutions that fit your requirements. It helps to work with an automation partner that understands your needs.
-
Rail Manufacturer Moves Full Steam Ahead with Safe, Efficient Workholding Solution
All World Machinery Supply paired a hydraulic power unit with remote operating capabilities in a custom workholding system for Ahaus Tool & Engineering.