GF Machining Solutions Platform Enables Remote Troubleshooting
The My rConnect provides a virtual link between a machine and the company’s service and support team, often eliminating the need for a technician to travel to a customer’s shop.
Share




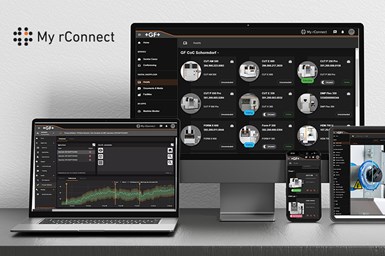
GF Machining Solutions (GFMS) has launched its new My rConnect platform engineered for the company’s EDM, milling and laser texturing machines. The platform enables shops to connect any model of GFMS machine for fast, responsive and easily accessible service and support while also providing expanded digital capabilities.
My rConnect is completely cloud-based; so as long as a computer is connected to the same network as their current GFMS machine, that machine is connected to My rConnect. However, GFMS machines that don’t have network access and are connected to the Internet can also use the software.
A key benefit of bypassing the need for a direct connection is security. My rConnect is password protected and includes an extended level of protection where the system verifies user identity via text message or email code.
The GFMS My rConnect provides a virtual link between a machine and the company’s service and support team, often eliminating the need for a technician to travel to a customer’s shop. When problems occur with those machines that are networkable, shops create an event for that issue, and a service engineer will log in and ask for permission to access and view the machine via the live Remote Assist function to diagnose problems at the machine level.
For nonnetworkable GFMS machines, the process is basically the same. However, once a GFMS service engineer connects using Remote Assist, the operator and GFMS service engineer can use My rConnect to communicate and resolve the problem.
From these types of service calls, GFMS can record data for how a particular service problem was resolved. If that same problem occurs but with a different customer, this data base of information enables the service engineer to quickly fix and/or diagnose the problem.
Within My rConnect, users can create groups, such as for the machines in various production facility locations. Once done, they can request any related documentation, such as manuals, for a particular machine. Instead of service having to send it, customers with My rConnect-connected machines can download needed documentation.
With a machine network connected to My rConnect, shops gain more digital capability. This includes access to current and future-developed applications that enhance the capabilities of customer machines, and the platform makes new or updated apps easy to acquire. GFMS can push the new apps or application update directly to a customer’s machines, notifying them when they log into a particular machine.
One such app is a new version of the company’s Job Recorder for wire EDMs and a version for its milling machines. The app lets shops record all the jobs they’ve done to generate efficiency reports based on how much time during the course of a day a machine worked on certain jobs.
Another app is the Machine Dashboard. It shows real-time machine status — whether it’s running, paused or off. For machines running, it shows the job being done and how long the machine has been working on it, in addition to all the previous jobs that have been processed on that particular machine and how long each of those have taken.
Related Content
Orthopedic Event Discusses Manufacturing Strategies
At the seminar, representatives from multiple companies discussed strategies for making orthopedic devices accurately and efficiently.
Read MoreContinuous Improvement and New Functionality Are the Name of the Game
Mastercam 2025 incorporates big advancements and small — all based on customer feedback and the company’s commitment to keeping its signature product best in class.
Read More2 Secondary Coordinate Systems You Should Know
Coordinate systems tell a CNC machine where to position the cutting tool during the program’s execution for any purpose that requires the cutting tool to move.
Read MoreCan ChatGPT Create Usable G-Code Programs?
Since its debut in late 2022, ChatGPT has been used in many situations, from writing stories to writing code, including G-code. But is it useful to shops? We asked a CAM expert for his thoughts.
Read MoreRead Next
AMRs Are Moving Into Manufacturing: 4 Considerations for Implementation
AMRs can provide a flexible, easy-to-use automation platform so long as manufacturers choose a suitable task and prepare their facilities.
Read MoreMachine Shop MBA
Making Chips and 91ÊÓÆµÍøÕ¾ÎÛ are teaming up for a new podcast series called Machine Shop MBA—designed to help manufacturers measure their success against the industry’s best. Through the lens of the Top Shops benchmarking program, the series explores the KPIs that set high-performing shops apart, from machine utilization and first-pass yield to employee engagement and revenue per employee.
Read MoreLast Chance! 2025 Top Shops Benchmarking Survey Still Open Through April 30
Don’t miss out! 91ÊÓÆµÍøÕ¾ÎÛ's Top Shops Benchmarking Survey is still open — but not for long. This is your last chance to a receive free, customized benchmarking report that includes actionable feedback across several shopfloor and business metrics.
Read More