Glebar's Electrolyte Tank Enhances Grind Management
The tank’s digital ultrasonic sensors connect with an I/O link to the HMI screen, which Glebar claims will enable better grind management, improved grind efficiency and reduced downtime.
Share





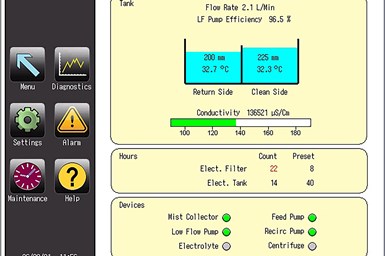
HMI screen displaying electrolyte health and fill level data as recorded by the enhanced sensors in the upgraded tank.
Photo Credit: Glebar
Glebar has developed an enhanced electrolyte tank that features digital ultrasonic sensors. The sensors feed data to connect with an I/O link to the human-machine interface (HMI) screen, which Glebar claims will enable better grind management, improved grind efficiency and reduced downtime. The upgraded tank provides users with a reliable way to check the electrolyte levels of their Tridex Electrochemical Cutoff and Grinding machines without having to do so manually.
Currently, operators monitor float hydrometers and perform visual inspections to measure the electrolyte salt density and fill levels. These are manual and operator-dependent processes that are said to provide an insufficient amount of data to accurately plan for electrolyte change and result in a lower process capability.
In the upgraded tanks, an I/O link switch connects digital ultrasonic sensors to the HMI screen which generates a graphical and numerical display of the electrolyte health and fill levels. This enables operators to make precise adjustments through a simpler and more accurate process. The alerts generated by the HMI enable operators to quickly make changes, which is said to result in less time spent troubleshooting.
Tom Travia, director of electrochemical grinding at Glebar, comments, “The digital ultrasonic sensors upload the electrolyte health data to the HMI screen, saving time and money.”
With the enhanced sensors and detailed display, Glebar says the new electrolyte tanks can reduce unplanned downtime, as well as increase throughput and process capability.
Related Content
-
Steady Culture, Flexible Plans Enable Custom Tooling Success
By late 2019, West Ohio Tool’s client list only spanned one page. The company overhauled its culture and is now on track for its most successful year ever.
-
M&M Quality Grinding Bars Support High-Volume Production
PMTS 2025: M&M Quality Grinding provides precision grinding services for a variety of materials, including titanium, stainless steel, alloys and plastics.
-
Seeking Custom Grinding and Automation with Weldon Solutions
Weldon Solutions is demonstrating three grinders at IMTS 2024. Though they differ in size and use case, all feature the company’s hallmark customizations.