Hainbuch Two-Jaw Module Clamps Cubic Parts
Hainbuch’s modular workholding system now includes a two-jaw module that can clamp cubic parts positioned centrically on machining centers and milling machines.
Share




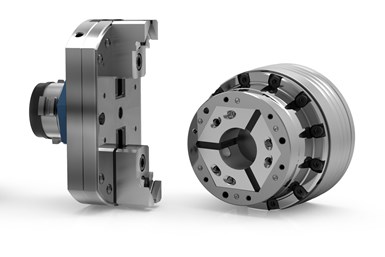
For users who work with a wide range of part diameters and configurations, as well as small quantities, the ideal setup is to have maximum flexibility. Hainbuch’s modular system is designed to handle round, prismatic, small and large components by allowing virtually any workholding configuration. Hainbuch’s designers and engineers in Germany are working to expand the modular system, and the company has now released a two-jaw module for clamping cubic parts.
The two-jaw module can clamp cubic parts that are positioned centrically on machining centers and milling machines. Users can change-over from clamping round parts to cubic ones in less than two minutes, according to the company. The module can also handle turning applications ranging to 1,500 rpm. Its compact profile makes it a good alternative to large, heavy centric vises.
The two- and three-jaw modules use the company’s collet chuck as their base. The Centrex quick-change interface enables users to perform change-overs without removing the collet chuck and realigning.
Because the modular system is smaller than many vises, it is less likely to interfere with machining. Applications may no longer require special, longer tools, and the risk of collision is reduced.
Related Content
-
How to Mitigate Chatter to Boost Machining Rates
There are usually better solutions to chatter than just reducing the feed rate. Through vibration analysis, the chatter problem can be solved, enabling much higher metal removal rates, better quality and longer tool life.
-
Quick-Change Tool Heads Reduce Setup on Swiss-Type Turning Centers
This new quick-change tooling system enables shops to get more production from their Swiss turning centers through reduced tool setup time and matches the performance of a solid tool.
-
Shoulder Milling Cuts Racing Part's Cycle Time By Over 50%
Pairing a shoulder mill with a five-axis machine has cut costs and cycle times for one of TTI Machine’s parts, enabling it to support a niche racing community.