Hypertherm Associates Software Supports Waterjet Cutting
ProNest LT will support virtually any make or model of a waterjet machine, enabling users to insert the nesting component into their existing workflow.
Share





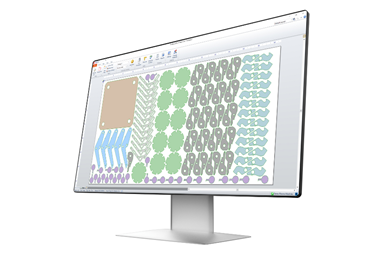
’ ProNest LT 2023 version 15.1 nesting software is available on a subscription basis for the waterjet cutting market.
According to the company, ProNest LT subscriptions for waterjet will support virtually any make or model of a waterjet machine, enabling users to insert the nesting component into their existing workflow.
There are two waterjet subscription tiers to choose from. The first, ProNest LT Omax, is specifically designed for Omax waterjet machines. Because both ProNest LT and Omax are part of the Hypertherm Associates family of brands, this tier was created in close collaboration with Omax engineers. It supports conventional, straight cutting for Omax machine models including OptiMax, Omax, Maxiem and GlobalMax.
The second option is ProNest LT Waterjet Plus, which is said to be a more comprehensive subscription tier. It supports conventional and straight cutting for virtually any waterjet brand, plus plasma and oxyfuel cutting, all in one package.
“With the price of raw materials rising, ProNest LT uses advanced, true shape nesting algorithms to help waterjet fabricators and manufacturers improve efficiency, get the most out of their material and lower costs,” explains Tom Stillwell, product marketing manager for the Hypertherm Associates Software Group. “Moreover, software that is based on a subscription model makes it easier to incorporate automation into existing workflows. It is easily scalable, enabling users to add features in accordance with their business requirements.”
Related Content
-
Flow Waterjet Systems Enable Complex Part Cutting
The Mach 200c enables bevel and five-axis cutting of most materials with up to 60-degrees of motion.
-
Omax Waterjet System Improves Efficiency, Precision
IMTS 2024: The Omax OptiMAX 60X waterjet system, equipped with optimized software and cutting capabilities, provides efficiency in production and precision.
-
Robot-Ready Laser Marking Machines Hit the Show Floor
Laser Marking Technologies LLC (LMT) is highlighting its robot readiness not only in its booth but also in its customers’ booths and partners Universal Robots and FANUC booths.