Next Generation of Heller's Horizontal Machining Center
Heller launched the fourth generation of its H series four-axis horizontal machining center, which offers Industry 4.0 features and more customization.
Share





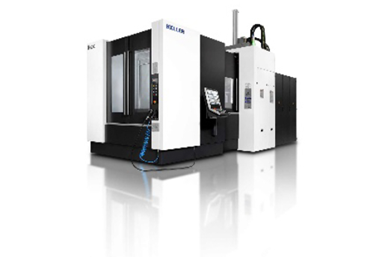
The H series horizontal machining centers were launched in early 2021 in the sizes H 2000, H 4000, H 5000 and H 6000 (pictured here).
Heller has launched the fourth generation of its H series of four-axis horizontal machining centers. This generation is said to offer shorter idle times, increased milling performance, reduced service times and more flexible customization to users’ requirements. It offers a modular design and is said to provide high basic accuracy and surface finishes.
The updates series includes ergonomic features such as a touch-sensitive operating panel comprising key functions, low loading sill, short overhangs and the possibility of overhead loading. Integrated LED lighting at the setting stations and inside the work area are standard.
The machining centers are available in sizes H 2000, H 4000, H 5000 and H 6000, covering a stroke range from 630 mm to 1,000 mm. The first two models are designed for tools with HSK-A 63; the larger ones are for tools with HSK-A 100.
Two drive technology equipment packages are available: Power and Speed. The Power package has been designed for medium batch sizes and the machining of steel and difficult-to-machine materials. The Speed package is suited for high-volume machining of cast iron, aluminum and other light metals.
The Speed package includes AutoSet technology cycle for weight-dependent dynamic adjustment of the Z-axis and B-axis, designed to optimize axis dynamics in correlation to the load capacity. It also features reduced spindle run-up times, which vary between 1.4 and 2.6 seconds, depending on spindle size.
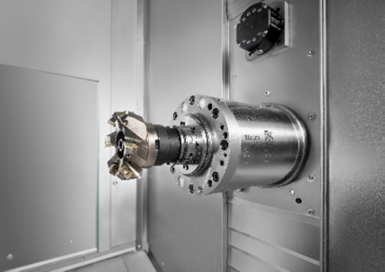
Heller spindles for the Gen4 machines are available in the known Power (PC), Speed-Cutting (SC) and now also in a Dynamic-Cutting (DC) version.
The in-house developed spindle for the Gen4 machines is available in three different versions: Power (PC), Speed (SC) and a new Dynamic Cutting (DC) version. All spindles are available with HSK-A 63 or HSK-A 100 tool holder. The DC units offer high torques and speeds, with the DC 63 i version providing 16,000 rpm and 180 Nm and the DC 100 i option delivering 12,000 rpm and 400 Nm. The U-axis of the Heller out-facing head allows users to perform contour turning operations on their components using motion tools.
This series is designed to offer reduced life-cycle costs. Speed-controlled pumps in the hydraulic unit and high-pressure portion of the coolant unit, smart switch-off strategies of energy consumers and the use of machine waste heat by optional water/water heat exchangers help ensure low energy consumption.
The main operating unit in panel design with double pivot arm is installed next to the work area door equipped with a large vision panel. The WorkCam work area camera allows the user to monitor processes throughout the work area on the 24” screen. The series also offers multi-touch technology as well as additional hardkeys and three potentiometers for the regulation of speed, feed and rapid traverse.
Users have access to Industry 4.0 features, including ‘Remote Diagnostic’ support; ‘Axis Condition’ and ‘Spindle Condition’ for predictive maintenance; ‘Tool Optimization’ for advanced data collection; ‘Energy Monitoring’; and ‘Damage Reduction’ for collision visualization.
All these HELLER4Industry features can be visualized directly at the machine, in the company network or online. Connectivity to MES and ERP systems has been expanded by OPC UA-based communication with the help of ‘umati.’ Users who select the Heller Services Interface (HSI) option get secure access to their production and maintenance data from any location in a browser-based solution.
Related Content
How to Mitigate Chatter to Boost Machining Rates
There are usually better solutions to chatter than just reducing the feed rate. Through vibration analysis, the chatter problem can be solved, enabling much higher metal removal rates, better quality and longer tool life.
Read MoreInside a CNC-Machined Gothic Monastery in Wyoming
An inside look into the Carmelite Monks of Wyoming, who are combining centuries-old Gothic architectural principles with modern CNC machining to build a monastery in the mountains of Wyoming.
Read MoreInverting Turning and Five-Axis Milling at Famar
Automation is only the tip of the iceberg for Famar, which also provides multitasking options for its vertical lathes and horizontal five-axis machine tools.
Read More4 Commonly Misapplied CNC Features
Misapplication of these important CNC features will result in wasted time, wasted or duplicated effort and/or wasted material.
Read MoreRead Next
AMRs Are Moving Into Manufacturing: 4 Considerations for Implementation
AMRs can provide a flexible, easy-to-use automation platform so long as manufacturers choose a suitable task and prepare their facilities.
Read MoreMachine Shop MBA
Making Chips and 91ÊÓÆµÍøÕ¾ÎÛ are teaming up for a new podcast series called Machine Shop MBA—designed to help manufacturers measure their success against the industry’s best. Through the lens of the Top Shops benchmarking program, the series explores the KPIs that set high-performing shops apart, from machine utilization and first-pass yield to employee engagement and revenue per employee.
Read MoreLast Chance! 2025 Top Shops Benchmarking Survey Still Open Through April 30
Don’t miss out! 91ÊÓÆµÍøÕ¾ÎÛ's Top Shops Benchmarking Survey is still open — but not for long. This is your last chance to a receive free, customized benchmarking report that includes actionable feedback across several shopfloor and business metrics.
Read More