Norton Ideal-Prime Grinding Wheels Increase Wheel Life
Norton’s Ideal-Prime Internal Diameter Grinding Wheels feature optimized, proprietary grains and matrices that lengthen wheel life and improve grinding and cost efficiency.
Share





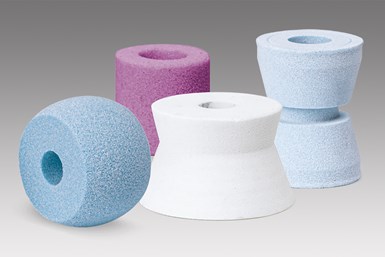
Norton Saint-Gobain Abrasives has introduced its high-performance Norton Ideal-Prime Internal Diameter Grinding Wheels for precision applications. The wheels feature Norton’s Quantum Prime nano-crystalline ceramic grain, embedded in a matrix of Norton Vitrium3 bond. The combination of the micro-fracture properties of the ceramic grain and the retention capability of the bond promotes long wheel life, improved grinding efficiency and consistent part quality with high-quality finish — resulting in 30% cost savings.
The self-sharpening grain technology increases the material removal rate and decreases the need for dressing — lowering cycle times and cost per part. Norton’s Quantum Prime grain technology also improves sharpness and cutting efficiency to reduce spindle power requirements, minimize mechanical stress and improve part geometry.
The grain micro-structure enables cooler cuts and maintains more stable wheel profiles and shapes, lengthening wheel life. Norton’s Vitrium3 bond technology also improves part surface finish.
“For customers demanding exceptional material removal rates in the highest tolerance precision applications, we are pleased to offer Norton Ideal-Prime Wheels,” says Kelly Pica, senior product manager for Norton Saint-Gobain Abrasives. “The combination of the innovative grain and advanced bond technology in our internal diameter grinding wheels provides an aggressive, free-cutting grinding solution with high productivity at a lower cost per part.”
Norton recommends its Ideal-Prime Internal Diameter Grinding Wheels for a range of applications including bearings, automotive, general engineering and gears. These wheels are available in grits ranging from 46 to 150, in grades from G to Q and in structures from 6 to 10.
Related Content
-
How to Mitigate Chatter to Boost Machining Rates
There are usually better solutions to chatter than just reducing the feed rate. Through vibration analysis, the chatter problem can be solved, enabling much higher metal removal rates, better quality and longer tool life.
-
Parts and Programs: Setup for Success
Tips for program and work setups that can simplify adjustments and troubleshooting.
-
Orthopedic Event Discusses Manufacturing Strategies
At the seminar, representatives from multiple companies discussed strategies for making orthopedic devices accurately and efficiently.