Hybrid Manufacturing in the Spotlight at Canadian Forum
Ontario manufacturer PTooling opened its doors for an additive manufacturing forum and open house to encourage the exchange of ideas regarding this disruptive technology.
Share





PTooling opened its Ontario shop to Canadian and international manufacturing professionals interested in additive manufacturing. A mural depicting some of the company’s key employees greets visitors just inside the door.
Manufacturers from Canada and the United States gathered at PTooling’s Amherstburg, Ontario, facility for an Additive Manufacturing forum April 27-28. Jointly hosted by Canada Makes and the WindsorEssex Economic Development Corp., the event included presentations from Marv Fiebig, president of PTooling; Dr. Gregory Hyatt, senior vice president and CTO of advanced solutions development for DMG MORI USA; and Matthias Kuehnelt of Hoedtke GmbH & Co. KG.
Mr. Fiebig focused his talk on what was, in many ways, the centerpiece of the event: PTooling’s DMG MORI hybrid manufacturing system. The machine combines five-axis CNC milling capabilities with a powder-fed laser deposition head to enable both additive and subtractive operations in the same cycle. The hybrid machine makes it possible to build additive parts up from scratch, as well as add features onto machined parts or repair damaged components.
PTooling’s became the first Lasertec additive manufacturing machine to be installed in North America when the company took delivery of it in December 2015. Now, it is one of three on the continent, but it remains the only one producing parts for external customers (the other two are captive machines owned by SpaceX and Boeing).
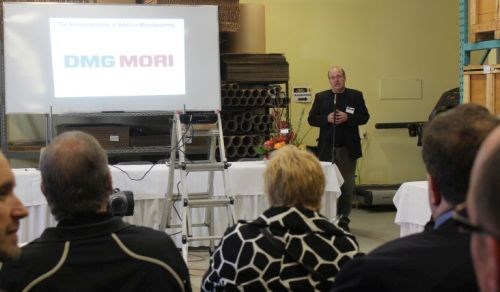
Marv Fiebig, president of PTooling, spoke to visitors about the company’s decision to purchase a hybrid manufacturing machine and the results it has seen so far.
Mr. Fiebig’s presentation described PTooling’s experience with the Lasertec hybrid and how additive manufacturing has affected its business. The company primarily serves the oilfield industry, but Mr. Fiebig says the new machine is opening up other possibilities in industries such as aerospace and plastics molding. He is also finding that new customers are now seeking out PTooling because of this capacity. Hosting the forum and open house was another way to help educate colleagues and potential customers about the technology.
Dr. Hyatt looked to AM’s future, drawing comparisons between additive manufacturing today and the automotive industry in the early 20th century and arguing that additive is on its way to being democratized similar to the way that automobiles eventually were. “We’re 80 percent of the way there,” he said, citing AM’s current capabilities to build on existing structures, incorporate multiple materials and integrate subtractive machining.
What will it take to achieve the remaining 20 percent? Cost per part must continue to come down and work envelopes must increase. Software that is easy to use and supports both AM and subtractive machining must be available. Robust machines that can handle 24/7 production must be developed. Dr. Hyatt also spoke to how DMG MORI is working to address these remaining concerns to help bring AM into production.

The Lasertec 65 3D has a laser deposition head fed with metal powder to additively build parts and features. The machine was running during the open house producing souvenirs for visitors.
Matthias Kuehnelt of Hoedtke spoke about the company’s research into best practices for hybrid manufacturing. Hoedtke, based in Germany, also owns a Lasertec 65 3D and has performed extensive testing on this machine with regard to both its additive and subtractive capabilities. Mr. Kuehnelt presented results from various tests exploring how parameters such as table movement and the direction of deposition affect the strength and quality of additive parts.
The event concluded with a Q&A session with the three speakers, and tours of PTooling’s facility. The organizers plan to make the additive manufacturing forum an annual event, and PTooling expects to host it again next year.
Related Content
Additive/Subtractive Hybrid CNC Machine Tools Continue to Make Gains (Includes Video)
The hybrid machine tool is an idea that continues to advance. Two important developments of recent years expand the possibilities for this platform.
Read MoreHow to Meet Aerospace’s Material Challenges and More at IMTS
Succeeding in aerospace manufacturing requires high-performing processes paired with high-performance machine tools. IMTS can help you find both.
Read MoreJTEKT Technology Days Showcases Synergies
The event took place following the company’s completion of its new showroom and decision to merge several of its brands under the JTEKT name.
Read MoreDesigning a 3D Printed Part with Machining in Mind
Designing extra stock and mounting features into a 3D printed part can aid in machining processes downstream.
Read MoreRead Next
AMRs Are Moving Into Manufacturing: 4 Considerations for Implementation
AMRs can provide a flexible, easy-to-use automation platform so long as manufacturers choose a suitable task and prepare their facilities.
Read MoreMachine Shop MBA
Making Chips and 91ÊÓÆµÍøÕ¾ÎÛ are teaming up for a new podcast series called Machine Shop MBA—designed to help manufacturers measure their success against the industry’s best. Through the lens of the Top Shops benchmarking program, the series explores the KPIs that set high-performing shops apart, from machine utilization and first-pass yield to employee engagement and revenue per employee.
Read MoreLast Chance! 2025 Top Shops Benchmarking Survey Still Open Through April 30
Don’t miss out! 91ÊÓÆµÍøÕ¾ÎÛ's Top Shops Benchmarking Survey is still open — but not for long. This is your last chance to a receive free, customized benchmarking report that includes actionable feedback across several shopfloor and business metrics.
Read More