ModuleWorks and Rafinex Synchronize Systems
In effective synchronization, topology optimization and toolpath planning enable more effective design-to-manufacture processes.
Share




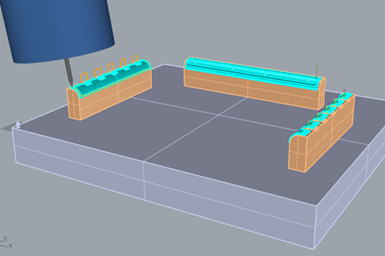
, developer of advanced numerical optimization software solutions, and ModuleWorks, developer of CAD/CAM software components, have integrated ModuleWorks’ toolpath calculation technology with the Rafinex software algorithm suite. In effective synchronization, topology optimization and toolpath planning enable more effective design-to-manufacture processes. This is reported to eliminate late change requests, avoid machining and robotic problems during the design phase and reduce engineering and manufacturing costs in subsequent processes.
Rafinex stochastic topology optimization anticipates real-life variability in material loads and material properties to help engineers design parts for high-performance applications in the aerospace and automotive industries, among others. The toolpath algorithms automatically calculate the optimal, material-independent toolpaths for different additive and subtractive processes (including robotic applications), which means manufacturing feasibility is analysed during design optimization.
"The accurate, effective and results-oriented approach of Rafinex is reflected in their projects and products”, says Lothar Glasmacher, head of additive & process technologies at ModuleWorks. “By combining ModuleWorks toolpath technology and Rafinex advanced optimization algorithms, we have significantly accelerated machine- and robot-based production processes."
In the next stage of their cooperation, ModuleWorks and Rafinex are incorporating inverse kinematics to calculate an optimal continuous toolpath for each component.
“Leveraging ModuleWorks’ toolpath planning in combination with our topology modelling software enables our customers to go a decisive step further and equally anticipate machining constraints and targeted cycle times when designing the optimal robust component,” says André Wilmes, CEO at Rafinex.
Using this synchronized workflow, engineers can identify design features that are too difficult or impractical to manufacture for any given production process and adjust the design accordingly. Spotting potential problems at this early stage can save considerable costs and speed up both prototype and series production.
Related Content
-
Automated CAM Programming – Is Your Software Really Delivering?
A look at the latest automation tools in Autodesk Fusion 360 software and how forward-thinking machine shops and manufacturing departments are using them to slash delivery times and win more business.
-
How to Mitigate Chatter to Boost Machining Rates
There are usually better solutions to chatter than just reducing the feed rate. Through vibration analysis, the chatter problem can be solved, enabling much higher metal removal rates, better quality and longer tool life.
-
Tips for Designing CNC Programs That Help Operators
The way a G-code program is formatted directly affects the productivity of the CNC people who use them. Design CNC programs that make CNC setup people and operators’ jobs easier.