Schunk Upgrades Low Maintenance, Quick-Change Jaw Chuck
Schunk says its Rota THW3 quick-change jaw chuck is particularly beneficial for users who produce small and medium quantities and are frequently switching between jobs.
Share





Schunk’s Rota THW3 quick-change jaw chuck is designed for short set-up times and low maintenance. According to the company, the Schunk Rota THW3 quick-change jaw chuck is particularly beneficial for users who produce small and medium quantities and are frequently switching between jobs.
The lathe chuck with the patented sealing system reportedly accelerates the jaw change on CNC lathes, pick-up lathes and turning-milling centers, while at the same time providing jaw change repeatability up to <0.02 mm. This means that jaw sets that have been turned out once can be used repeatedly, even with demanding tolerances.
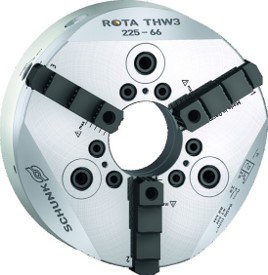
The jaw stroke of the straight toothed base jaws is 6.7 mm to 10.5 mm, depending on the size. A ring piston with a direct power transmission is said to ensure a high degree of efficiency, and in the smallest size, 200, the chuck already achieves a clamping force of 64 kN; from size 400 it is 240 kN. Its hardened and stiff base body ensures that precise and reliable machining can be carried out even under maximum stress. The jaw features a large chuck bore from 52 mm (size 200) to 165 mm (size 630), protective rifles that can be exchanged from the front and the possibility of internal and external tension. There is also the option of supplementing the chuck with an adjustable stop.
The Rota THW3 chuck has also been enhanced with large tool storage, multi spindles and modular machine controls. The company says these enhancements enable faster throughput, flexibility and accuracy.
Matching chuck jaws for the Schunk Rota THW3 chuck can be found using Schunk’s chuck jaw quickfinder. The user can choose from a list of all matching chuck jaws from over 1,200 jaw types.
Related Content
-
Five Common Mistakes Shops Make with ER Collets (And How to Prevent Them)
Collets play a crucial role in the machining process, so proper tool assembly and maintenance is important. Here are five potential pitfalls to avoid when using ER collets.
-
The Future of High Feed Milling in Modern Manufacturing
Achieve higher metal removal rates and enhanced predictability with ISCAR’s advanced high-feed milling tools — optimized for today’s competitive global market.
-
Briquetting Manufacturer Tools Up for Faster Turnaround Times
To cut out laborious manual processes like hand-grinding, this briquette manufacturer revamped its machining and cutting tool arsenal for faster production.